

affordable living - OUR MARKET!
Housing construction forms the central core business of MODULAB.
Looking at the tense situation on the housing market in all German regions, the subject of "affordable housing" is right at the top of the political agenda. The construction of affordable housing is therefore more important than ever and initiatives
like the federal government's housing offensive have the aim to meet the high demand for affordable housing in the short term and for as long as possible.
MODULAB has analyzed the funding guidelines of all banks and institutions of the federal states in Germany and
developed the 'MODULAB Matrix' so that the MODULAB M-SERIES modules meet all necessary funding requirements.
The apartments planned by MODULAB are therefore fully compatible with all rules governing subsidies for rental housing construction, in all german federal states.
In addition, MODULAB places a special emphasis on wood as a building material. Many cities, like Hamburg, subsidize this seperately. The higher the proportion of wood in the construction of the building for new, inexpensive rental apartments, the higher the subsidy amount.

Project: Apartment building in Neustadt am Rübenberge I Completion summer 2021
your project - OUR SERVICES!
MODULAB generally offers 2 different options for execution of residential construction projects with the M-SERIES modules:
-
Extended shell construction: all modules for the building as well as the exterior facade and roof and all planning services. Interior finishing of units is excluded.
-
General contractor: The entire building will be completed on a turnkey basis.
The decision to commission MODULAB as general contractor for a turnkey construction project means there is only one contact, fixed prices, planning security, short construction times and adherence to deadlines due to the weather-independent construction!
MODULAB carries out most of the work on the construction site with long-term employees and also works exclusively with reliable and competent subcontractors.
The coordination and monitoring of the external trades is the sole responsibility of MODULAB.
simple way - OUR PLANNING PROCEDURE!
...1
First meeting with our project advisor.
We recommend a plot of at least 1,500 square meters
... 2
Analysis of the data in our M-Series software
Property size GRZ / GFZ
Site plan / development plan / alignment
... 3
Initial Assessment for planning and implementation
Basic determination to implementation planning
... 4
Construction and construction phase planning
Production planning (modules) and project-specific construction planning

... 7
Exterior work and handover
facade
gardening
handover
... 6
Building modules on the construction site
followed by roof modules
roof tiles
... 5
Production of modules in the module factory
parallel poring of concrete foundations, staircases and technical services, utilities
more than the sum of all parts - THE M-SERIES
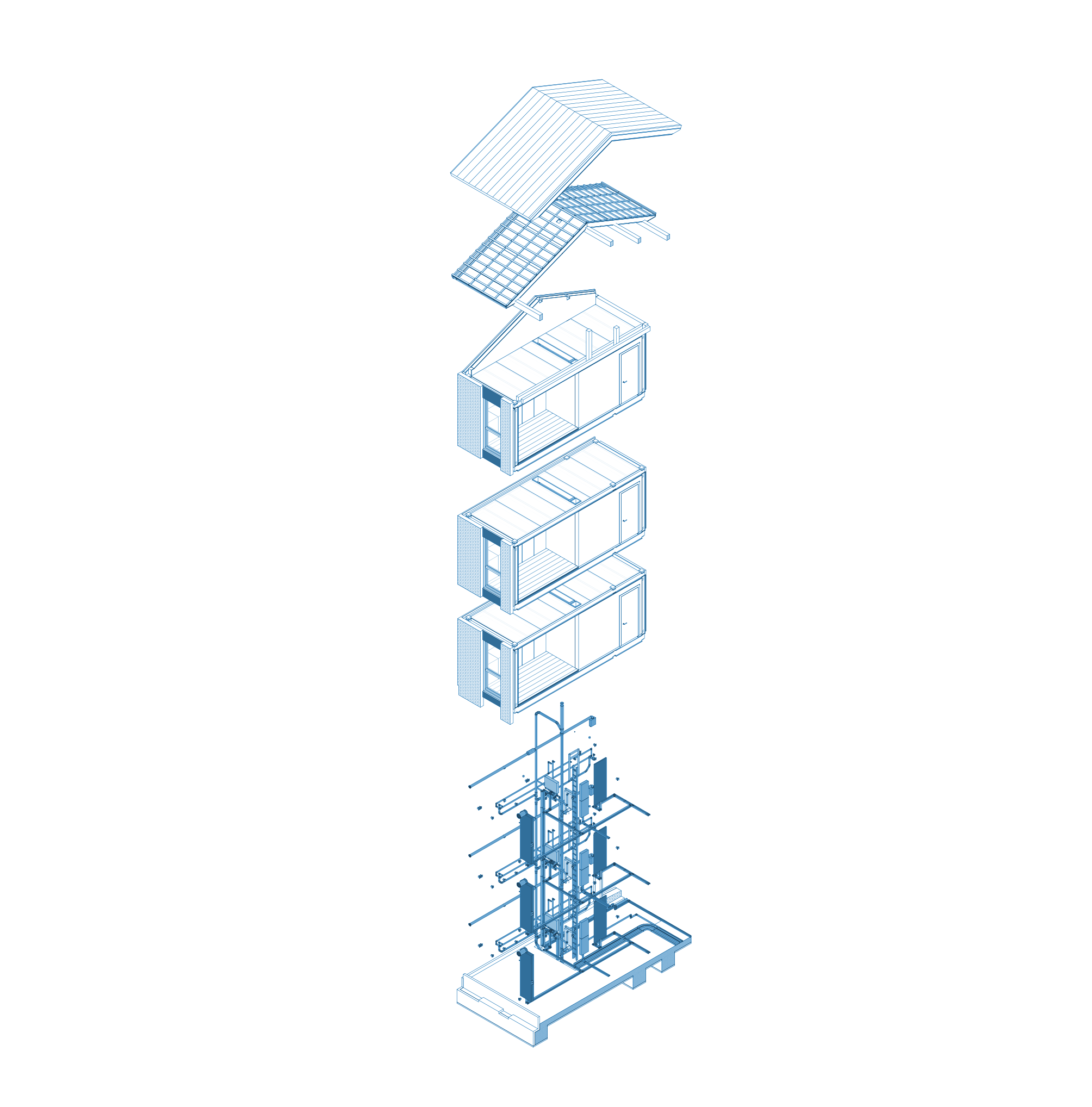
Our components are designed in such a way that the smallest possible number of modular elements results in the greatest possible freedom in flat configurations . This saves manufacturing costs and still enables unlimited freedom
in the different building options .
Out of a total of 28 components, MODULAB and our design team have developed 5 modules (M-SERIES) which, in combination
result in a large variety of possible floor plans. The smallest apartment with 1 bedroom, bathroom and kitchen-living room
is 47.9 square meters and grows by approx. 15 square meters with each additional bedroom.
You can find more information on possible floor plans in the download area .
MODULAB builds industrially and modularly using a timber frame construction . This is a modern, healthy and flexible
construction method that leaves a lot of flexibility in terms of design.
In the timber frame construction, the walls of the module are cladded on both sides with wooden panels after the required insulation and moisture - barrier has been placed inside.
With this so-called planking, the individual elements such as the wall, ceiling or roof are stiffened in order to achieve the desired strength rsp. statics of the build.
A great advantage of this type of modular construction is that the manufacturing of wall, ceiling and roof elements are
done in our production hall. Then the individual assembly of modules is completely independent of the weather
conditions outside. The ready-to-install modules are put together on the construction site.
This shortens the construction time by approx. 70% compared to conventional construction methods. MODULAB can complete a building with 6-10 apartments within a week. Since the timber frame construction is a dry construction method, there are also no drying times. The interior work can start immediately after the modules are placed onsite, provided
unless modulab has not already completed this as part being general contractor.
Thanks to the certified industrial factory production, a higher quality standard can be achieved compared to many conventional construction methods.
All buildings can be delivered turnkey or ready-for-final-finishing
A brochure on the subject of about the M-SERIES can be found in the download area .
Topic - SUSTAINABILITY

Ecological quality
Wood as the basis of the modular building construction is a regenerative building material
with a closed material cycle and is 100% recyclable and CO2 neutral which guarantees the sustainability of resource management. High heat
insulation and constructions free of thermal bridges ensure optimal
Energy efficiency of the modular building, which in turn strengthens sustainability.
Socio-cultural quality
Energy efficiency and cozy comfort are achieved through high thermal insulation and the thermal bridge-free construction of the modular building - cozy warmth in winter, pleasant coolness in summer, sustainability without waste.
Technical quality
Modular buildings meet the highest demands on heat, fire and sound insulation and are made from quality-tested German branded products. In terms of durability, they are in no way inferior to conventionally constructed buildings. In contrast to conventional construction, modular buildings can also be dismantled without leaving any residue.
Economic quality
The industrial production and the certified production processes guarantee a consistently high quality of the modular buildings, which cannot be achieved with conventional buildings. The up to 70% reduction in construction time allows early use and a faster return on investment.

Fire protection
The country-specific requirements and standards for fire protection, such as DIN 4102, are met in the standardized modulab modular building. The results are proven time and again by independent reports from renowned fire protection institutes.
Soundproofing
As a result of the system, our modular buildings have very good sound insulation. The respective sound insulation requirements can be achieved through the double-shell wall and ceiling system. The sound insulation values measured on the implemented modular building, both in the ceiling area and in the partition wall area, are usually significantly better than the legally required values.
heat protection
In terms of thermal insulation, modulab modular buildings naturally meet all requirements of the applicable country-specific standards. The high level of component insulation with the corresponding physical properties of the insulating materials and the construction without thermal bridges play an important role in this context.
Indoor air hygiene
On average, people spend up to 90% of the day indoors. The quality of the indoor air therefore plays an important role for general well-being and in the context of preventive health protection. Only tested, low-emission materials are used in the modular building from modulab. The VOC and TVOC values in the modulab modular building are well below the relevant guide values and normal indoor air concentrations.